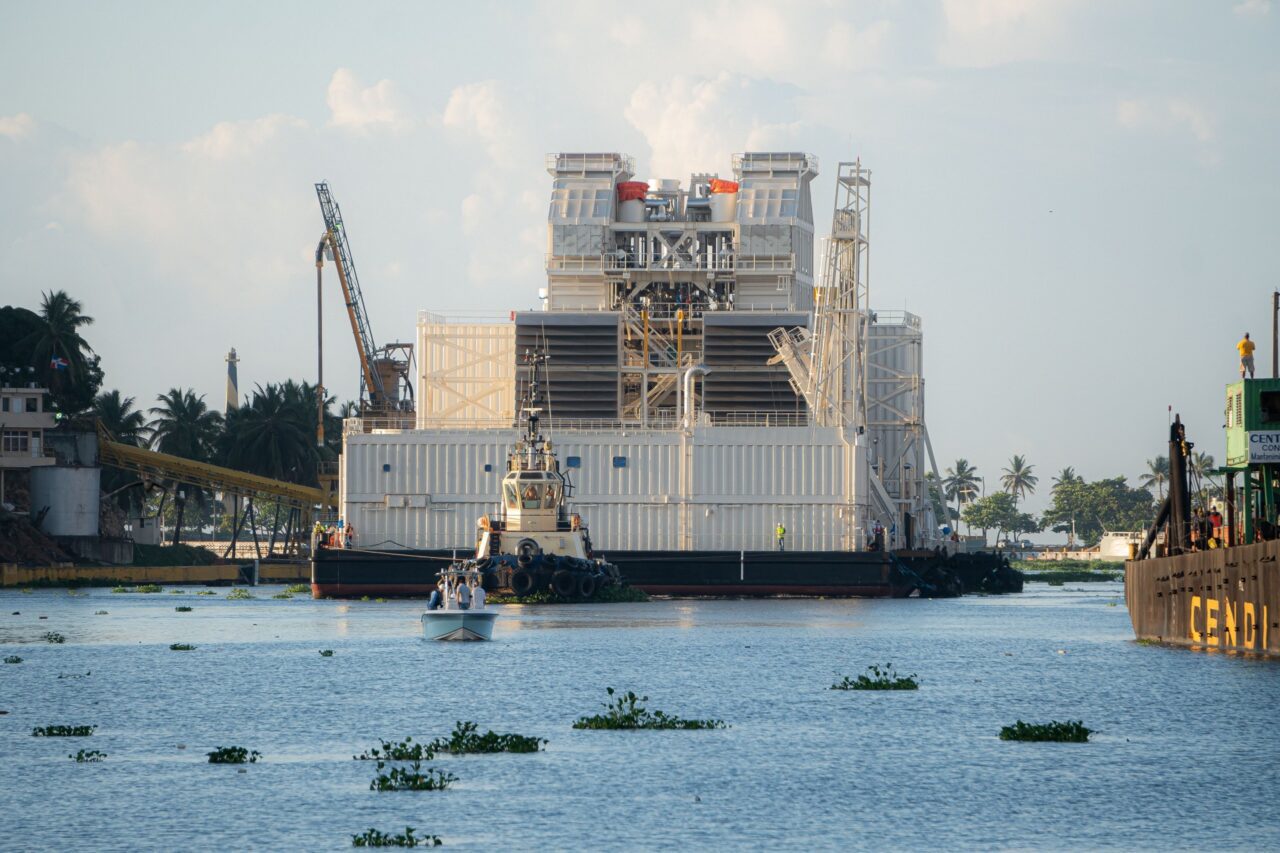
Gas power technology developers are exploring new roles and applications to ensure gas power will remain relevant as power markets embrace decarbonization.
At the end of 2020, about 1,600 GW of gas turbines were installed globally, the vast majority of which burned natural gas or methane for electricity generation. While high-level outlooks generally suggest natural gas will continue to flourish as the largest source of power in advanced economies over the next decade, a broader push for net-zero emissions could send the resource into long-term decline.
To stay relevant amid the anticipated proliferation of renewables, energy storage, and decarbonized gas, the gas turbine industry is readying for a spate of emerging applications. Along with increased hybridization with renewables and storage, turbine makers are exploring combusting low-carbon fuels; ramping up turbine efficiency, performance, and operational flexibility; and ultimately, reducing their carbon output.
Multiple Approaches to Power-to-X-to-Power
Meeting these attributes will require strategic collaboration on all fronts, including in technical areas, notes ETN Global, a Brussels-based nonprofit trade group representing the entire gas turbine technology value chain. Spearheading a notable European Union (EU)-backed project that explores multiple approaches, 21 ETN Global members—which span energy utilities, technology companies, academic institutions, and other gas turbine stakeholders from 10 countries—in April 2020 kicked off a four-year project called “FLEXnCONFU.”
FLEXnCONFU’s ultimate goal is “to develop and demonstrate innovative, economically viable and replicable Power-to-X-to-Power (P2X2P) solutions that combine all available options for the effective and flexible use of surplus power from renewable energies to level the power plant load by converting electricity into hydrogen or ammonia prior to converting it back to power,” explained Alessandra Cuneo, a project manager at RINA Consulting, who serves as FLEXnCONFU’s project coordinator. “This will enable the design and operation of an integrated power plant layout that can unlock additional [combined cycle gas turbine (CCGT)] flexibility,” she said.
The consortium, which has a total budget of $ 14.4 million (€12.6 million), plans to complete several milestones under four “pillars” by FLEXnCONFU’s conclusion in March 2024: The use of non-conventional fuels in CCGTs for flexibility and sustainability; the integration and demonstration of power-to-X systems in a real power plant; the development of an advanced control system dedicated to enhance CCGT flexibility and grid interoperability; and the promotion of a hydrogen and ammonia energy society.
One notable objective is to demonstrate—at a technological readiness level (TRL) 7—a power-to-gas-to-power (P2G2P) solution developed by Cummins’ Hydrogenics and Italy’s ICI at one of the three Siemens V94.3A CCGTs at EDP’s 1.2-GW gas-fired Ribatejo power plant in Portugal. Separately, FLEXnCONFU will target 1,000 operating hours for a power-to-hydrogen demonstration at the Ribatejo plant starting in April 2023.
In another project, project partners are targeting a TRL 6 for a power-to-ammonia-to-power (P2AP) solution developed by Dutch firm Proton and ICI that will be demonstrated at a modified micro gas turbine operating at a University of Genoa laboratory in Savona, Italy. The P2G2P solution will be directly controlled by a grid-driven/responsive management system developed by automation firm MAS Controlling Power & Energy, and gas turbine combustion acceptability of different natural gas, hydrogen, and ammonia mixtures will be studied in Cardiff University labs.
Essentially, FLEXnCONFU will be a “demonstration-to-market project,” said Simon Gianordoli, project officer at ETN Global. After the project has been completed, these technologies will be upscaled and replicated at CCGTs owned by ENGIE Laborelec and Tirreno Power. Ultimately, ETN Global hopes FLEXnCONFU “will enhance the possibility of CCGTs offering services on the ancillary services market, guaranteeing a more secure, clean and resilient power system,” he added.
Adapting to an Extended Fuel Spectrum
Outside of this collaborative space, every major original equipment manufacturer (OEM) seems to recognize that gas turbine fuel flexibility could open up a competitive edge and add market value as the world trundles deeper into decarbonization. Many are adapting their machines to unconventional fuel resources (such as biofuel, shale gas, and liquefied natural gas) and low-carbon fuels, including hydrogen and ammonia. Hydrogen, notably, has grown into a developmental priority, and some OEMs have even laid out roadmaps to get to 100% hydrogen combustion for a majority of their fleets.
![]() |
1. Mitsubishi Power’s M501JAC model is a simple cycle gas turbine, ISO-rated at 425 MW at baseload output, and 44% efficiency on natural gas fuel. A single-shaft 1×1 combined cycle plant is rated at 630 MW net plant output at more than 64% efficiency. Courtesy: Mitsubishi Power |
Much development has so far focused on dry-low nitrogen oxide (DLN) technology advancement, using lean-premixed or multi-cluster combustion technologies to control nitrogen oxide (NOx) emissions, and achievements are already translating into project deals. Mitsubishi Power, which in May 2020 snagged a contract for two 1×1 M501JAC (Figure 1) CCGTs for the 840-MW Intermountain Power Plant in Delta, Utah, commercially guaranteed that the gas turbines will combust a mix of 30% hydrogen (by volume) and 70% natural gas fuel when they go online in 2025. The contract requires that the plant’s hydrogen capability will transition to 100% hydrogen by 2045, enabling its operator and majority power purchaser, Los Angeles Department of Water and Power, to meet California’s stringent climate goals.
As Michael Ducker, senior vice president and head of Hydrogen Infrastructure at Mitsubishi Power, told POWER, the company has made headway on its DLN multi-cluster burner. Many more “customers are looking at, by the late 2020s and 2030s, gas turbines being able to operate on 100% hydrogen,” he said. “They’re starting to scope out projects, wanting that capability built-in today,” he said. “Mitsubishi Power, from a product development standpoint, is on track and supportive of these projects.”
Some industry experts, however, caution that banking on hydrogen combustion as a replacement for natural gas to achieve decarbonization will come with crucial challenges. One especially under-reported concern is that hydrogen’s heating value and density are small compared to natural gas, said Diane Fischer, director of Generation Services at Kiewit Engineering.
![]() |
2. Co-firing with hydrogen or firing 100% hydrogen by volume could have a marked effect on a natural gas–fired power unit’s capacity. Courtesy: Kiewit Engineering |
“If you go to 100% [by volume] of hydrogen, that combustion turbine, from a thermodynamic calculation perspective, is going to be about at 30% capacity of the original combustion turbine as fired with natural gas,” she explained. “That’s entirely a function of the heating value and the density of hydrogen compared to natural gas. So, if you want to accomplish the same thing with hydrogen, you’re going to need to put in a lot more hydrogen than you would need to put in with natural gas,” she said.
Conversely, “to get to the same capacity as you have with natural gas, you’re going to be well over 200% of the volume that you originally had to accomplish the same goal” (Figure 2). Along with combustors designed for these larger volumes that will likely be needed for units firing mostly hydrogen, hydrogen combustion may require more downstream NOx control, and faster ignition speeds may be challenging for units that will vary their fuel mixes, she said.
Operating and maintaining a hydrogen-fired gas turbine may also prove challenging. While typical natural gas units tamp down the pressure of pipeline gas using pressure reducers suitable for their combustion turbines, hydrogen supplies, whether from an electrolyzer or a delivery, will need to be stored and pressurized, much like calibration gases, Fischer said. Other supply risks include potentially unreliable supplies and system requirements uncertainty. Gas generators (see sidebar) will also need to comply with certain hydrogen-related safety design codes, including for fire protection, venting, piping, and pipelines.
Carbon Capture Growing More Attractive
Because low-carbon fuels may be better suited to regions that have “young” thermal fleets (and which have access to hydrogen and ammonia), gas power’s future may be more deeply entrenched in its ability to abate its carbon emissions, and integrate carbon capture, utilization, and storage (CCUS) systems. Interest in CCUS for gas generation is growing, albeit gradually. As of November 2021, only 15 of an estimated 40 developing power projects with CCUS were gas-fired.
Projects like SSE Thermal and Equinor’s Keadby 3, a 910-MW CCGT project in North Lincolnshire in the UK, are being closely watched. Slated to come online in 2027, the natural gas–fired project will feed hot flue gases to an integrated carbon capture and compression plant to capture at least 90% of its emitted CO2.
In the U.S., where several CCUS projects are bolstered by tax incentives, the government in October granted $ 45 million to 12 natural gas projects as part of efforts to address point-source carbon capture. Among them is a project to equip Calpine’s 1.1-GW Deer Park CCGT facility in Texas with Shell’s Cansolv CO2 capture solution, a technology that has been in operation since 2013 at SaskPower’s Boundary Dam project.
GE Gas Power will also notably get $ 6 million to complete an engineering design study to incorporate a 95% commercial carbon capture solution into an existing CCGT site at Southern Co.’s Plant Barry in Alabama that will provide advanced operability, lower costs, and high efficiency. The solution is expected to be scalable to other commercial sites. Also, much-watched are several commercial projects that will feature NET Power’s Allam cycle. The Allam Cycle uses CO2 as a working fluid in an oxyfuel supercritical CO2 power cycle, producing a relatively pure CO2 stream “at a significantly lower capture cost.”
An Efficiency Penalty
Equipping gas-fired plants with CCUS on a wide scale, however, may be nuanced and rife with challenges, noted GE Power Decarbonization Director John Catillaz and Emergent Technologies Director for Decarbonization Jeffery Goldmeer. “There are two ways to systematically approach the task of turning high efficiency gas generation into a zero or near zero-carbon resource: pre- and post-combustion,” the GE experts recently explained. “Precombustion refers to the systems and processes upstream of the gas turbine. The most common approach today to tackle pre-combustion decarbonization is simple: change the fuel.” On the post-combustion side, “a tool chest of different technologies that can remove CO2 from the flue gases” is used. In order for the power sector to rapidly decarbonize while maintaining high levels of reliability, GE believes “both pre- and post-combustion decarbonization options for gas turbines are viable tools available today,” they wrote.
But, “[a]s with most things in life, rarely is there any free lunch,” they warned. A glaring issue is that the thermodynamic cycle of the amine system requires thermal energy, which in a CCGT plant would be taken from the heat recovery steam generator (HRSG) or the steam turbine, depending on the required conditions. “Historically, the associated efficiency penalty has been calculated to be rather high at almost 10 points of combined cycle efficiency.” However, reassessments have recently “uncovered the possibility of reducing the penalty by improving the steam and carbon capture processes,” they suggested. For example, “GE’s analysis of a 2 x 1 combined cycle 7HA plant (~1,200 MWs) indicated the efficiency penalty is closer to 6% at an 85% carbon capture rate.” Still, though more work on the issue is ongoing, the authors concluded “there is no avoiding an efficiency penalty.”
Another prominent challenge is “not every asset will be considered a good candidate due to multiple factors, including available land, access to geologic storage formations, and lack of policy/regulations to encourage deployment,” they said. Costs are also a big concern: “An approximate rule of thumb for a 90% post-combustion carbon capture system is that it can double the capital expense of the power plant. Nominally, this is certainly a significant investment. But unlike efficiency losses, which are linear to the amount of carbon reduction, it is important to keep in mind that capital expense does not have a linear relationship with the percentage of carbon reduction,” the experts noted. “Therefore, moving down to an 85% carbon capture rate sees a very significant reduction in capital cost.”
Existing projects should still explore CCUS as part of retrofit strategies, given that it may help “de-risk future carbon regulations that impact the decision to build a gas-fired power plant today,” they added. “Additionally, costs can be reduced even more so on new power plant builds due to synergies of construction operations, onsite equipment and labor, etc.”
The Flexibility of Floating CCGTs
In an effort to capture new markets, developers have for decades offered floating power plants—typically vessel-mounted diesel, gas, or dual-fuel engines—because they can be built cost-effectively and rapidly. Because they are mobile, they can be relocated or traded, and because they do not require a large site and sometimes have no land footprint, they can be deployed even in the most remote locations and under challenging ambient conditions, both for temporary or permanent power.
So far, however, most gas turbines installed on floating production storage and offloading (FPSO) and oil and gas (O&G) platforms have been open/simple gas turbine modules, mainly to take advantage of their high power density and increased availability over gas engines and diesel gensets. But as more offshore operators commit to more stringent environmental targets, Siemens Energy sees an opportunity for its “ultra-light combined cycle” (ULCC) and “ultra light bottoming cycle” (ULBC). The cycles are designed for a floating CCGT power plant concept that the company has integrated into its “SeaFloat” product.
Designed like a typical gas turbine used in the oil and gas industry—like Siemens Energy’s SGT-A35 and SGT-750 gas turbines—the ULCC consists of the gas turbine package, steam turbine package, once-through heat-recovery steam generators (OTSG), and the related balance of plant. The ULBC is designed for steam-tailing only behind existing gas turbines, explained Hamed Hossain, a Siemens Energy’s SeaFloat Business Owner. “Therefore, it’s available for new-build applications and for optimizing existing assets.”
A major achievement in the floating plant’s design is its weight and footprint. “It’s obvious that weight and footprint play a major role on FPSOs and [oil and gas] platforms resulting in lower steel requirements and allocated space requirements. The weight of the ULBC is approximately 50% lower than typical offshore combined cycle plants,” Hossain told POWER. “In this case, climate protection goes hand-in-hand with significant economic benefits in view of carbon taxes and licenses that are required in more and more countries.”
However, SeaFloat’s value proposition for power generation is “multi-faceted,” he noted. “SeaFloat provides new and clean combined cycle technology to areas where land is not available or where land rights are a challenge or simply too costly. It embodies the highest possible form of modularization: The power plant is provided in one piece to the desired location as a mobile asset or for permanent installation,” Hossain added. “It’s not just about land, it’s also about substituting aged assets like reciprocating engines, diesel generators, and coal-fired power plants with highly efficient technology based on our state-of-the-art SGT-800 gas turbine.” While carbon reduction is a key design attribute, SeaFloat may also slash other pollutants like NOx, carbon monoxide, and nmHC by up to 90% compared to reciprocating engines.
“These value propositions deliver many benefits for our customers with different requirements,” Hossain said. The concept, for example, could furnish many assets that are still running on heavy fuel oil with options to run on liquefied natural gas (LNG). “Therefore, the SeaFloat power plant’s high efficiency plays a major role in the business model of LNG-to-power projects. The SeaFloat power barge can be served from a floating storage and regasification unit (FSRU)—or a fully integrated solution FSRP along with an LNG storage and regasification unit can be provided anywhere in the world that lacks access to clean fuel,” Hossain said.
Today, SeaFloat projects under development around the world are also targeting “the entire Siemens Energy value stream,” including SeaFloat, battery energy storage, hydrogen generation, and transmission solutions. This “holistic approach” is geared to help customers “find the right energy mix that will prepare them for the future today,” Hossain said.
The latest SeaFloat project, for example, is the 145-MW Estrella del Mar III power station (Figure 3), which is currently being deployed in the Dominican Republic. The plant design was conceived by Siemens Energy’s engineering and manufacturing team in Sweden, along with vessel design performed by ST Engineering. “To maximize space utilization, each component is optimized with regard to function and footprint—e.g. the best-in-class gas turbine, SGT-800, is used as a pre-assembled single lift complete package with a small footprint. Additionally, the equipment is exposed to sea movement (roll & pitch), which required structural reinforcements affecting the overall layout and barge deck characteristics,” Siemens Energy said.
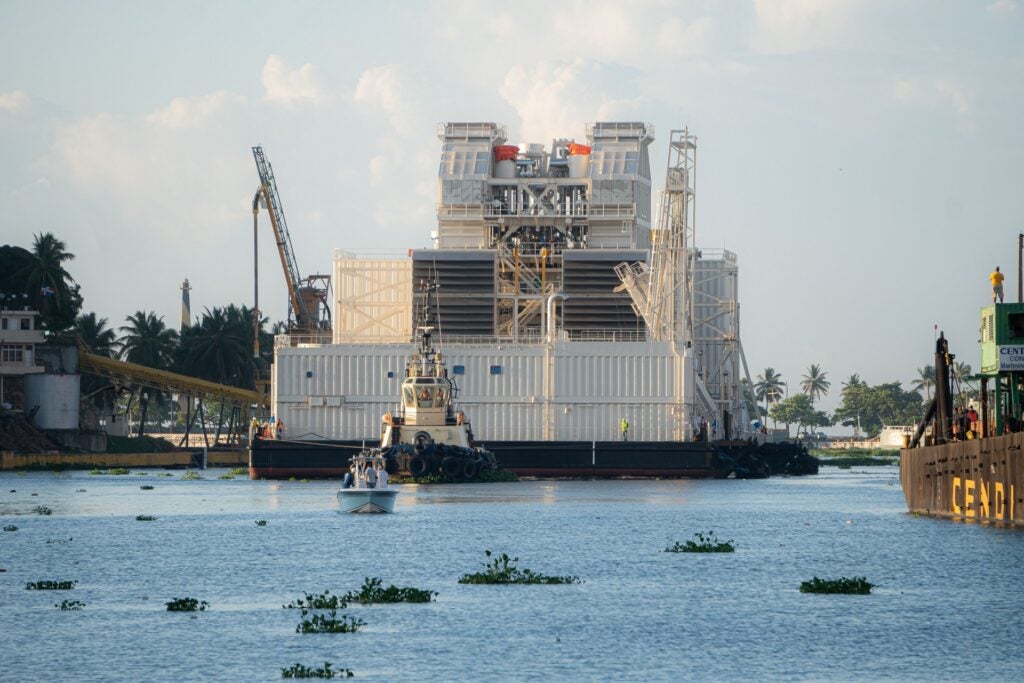
Estrella del Mar III, notably, also includes a battery energy storage system to compensate for power shortages and frequency drops on a grid. “Overall, the barge provides optimal space utilization and high-power density. Furthermore, the concept is being continuously optimized by the SeaFloat team to improve weight, space, efficiency, emissions and to be an integral part of the global energy transition to decarbonization and decentralization,” the company said.
—Sonal Patel is a POWER senior associate editor (@sonalcpatel, @POWERmagazine).
The post New Realms for Gas Power Technology appeared first on POWER Magazine.