The post Power Line Management in the Time of Coronavirus appeared first on POWER Magazine.
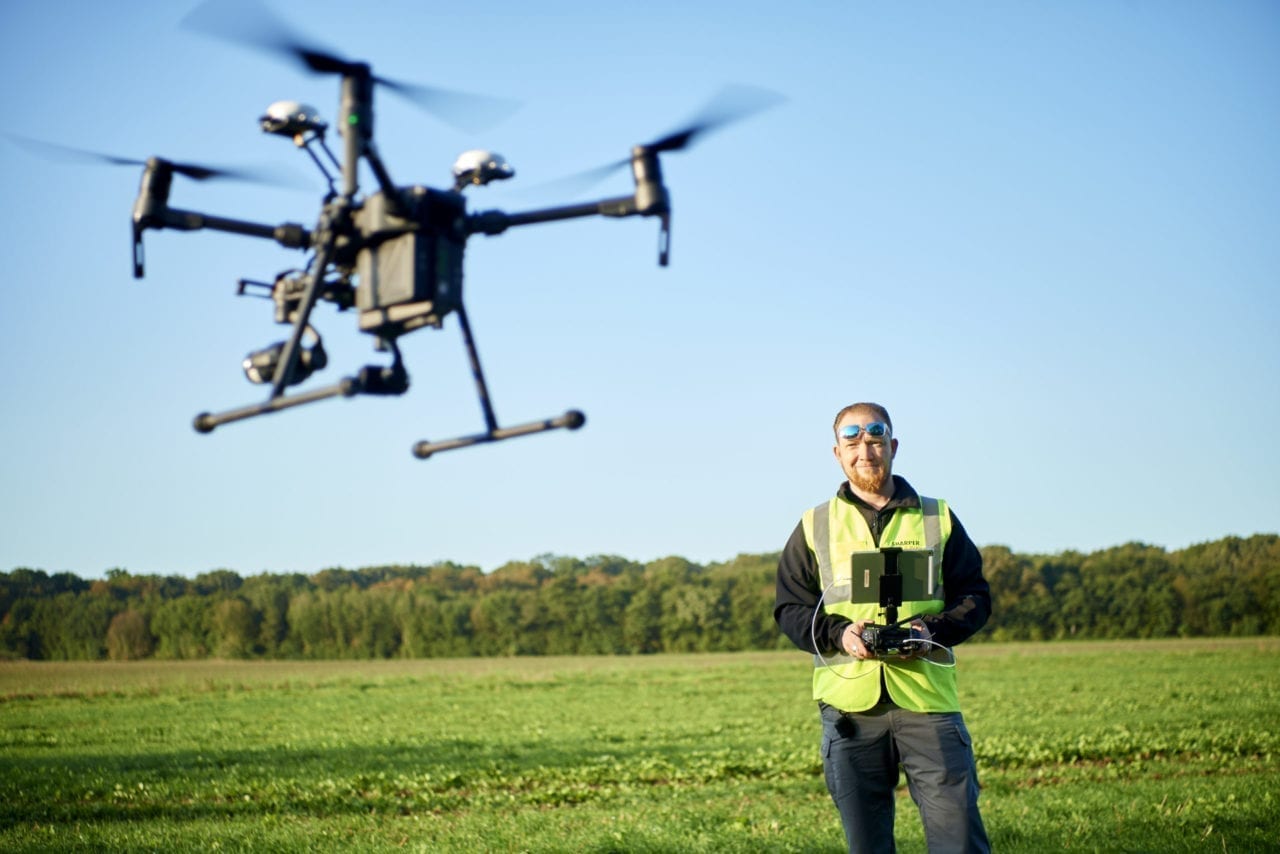
The novel coronavirus (COVID-19) has put communities on lockdown and created a need for social distancing. Many are staying at home, but that’s not an option for the frontline workers running critical power transmission infrastructure and keeping the lights on.
How can utilities keep up with their operational and safety obligations with a reduced onsite workforce? Specifically, how can utilities maintain power line inspection and maintenance regimes, and what are the additional challenges for those in areas such as California, where COVID-19 collides with other threats, such as wildfire season?
Making Hard Work of Field Work
By definition, power transmission and distribution networks deal with long distances. At the best of times power line inspection entails despatching crews into the most remote pockets of a country or state, far from major population centres.
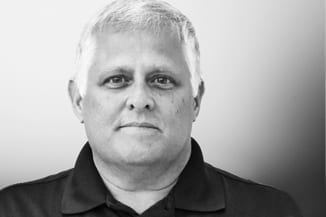
In many ways that can be a blessing: deep in the forests and mountains you may be more likely to run into a cougar or bear than another human being carrying COVID-19. However, the virus does bring logistical challenges.
For example, for jobs remote enough to require overnight stays, where do inspectors turn when hotels are closed due to shelter-in-place rules? In some instances, an Airbnb may be an option, but care must be taken to ensure employees can observe social distancing rules, which can limit the number of team members sharing a hotel or Airbnb.
Of course, the biggest threat of coronavirus is to people. Every utility we have talked to has rightly placed priority on safeguarding their employees’ health and safety, minimizing people required onsite. It may also well be that a number of staff—even if they do not fall ill themselves—will have to self-isolate or care for a family member. Utilities must factor in reduced head counts alongside the logistical challenges of maintaining social distancing among those at work.
Taking Remote Control
Fortunately, these aren’t unsolvable problems. The pandemic has hit at a time where technology has progressed such that it can provide some solutions.
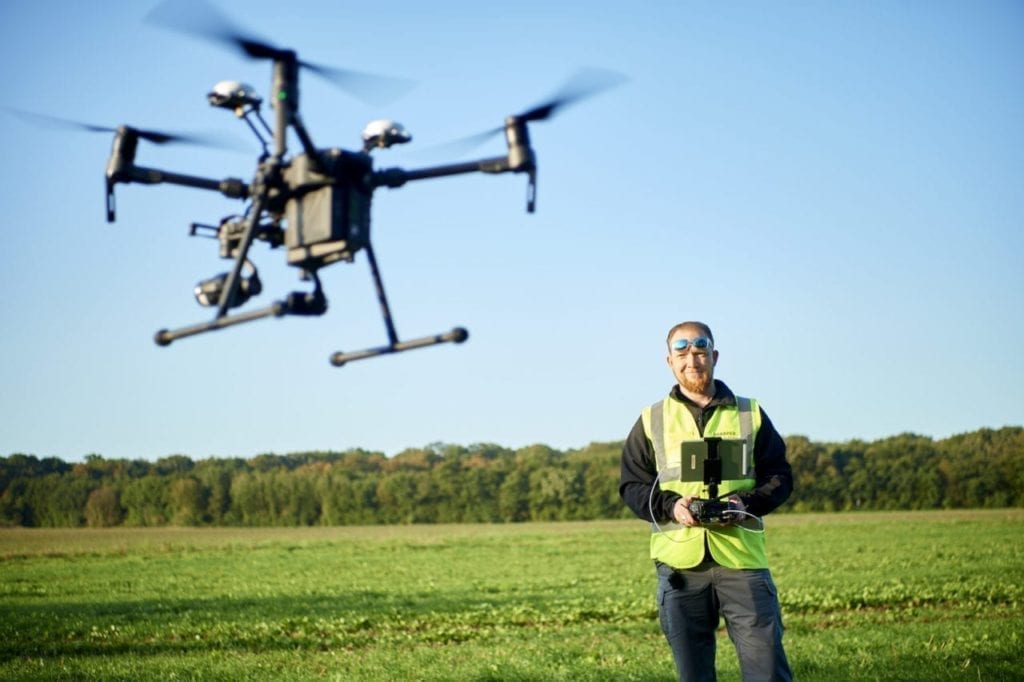
In recent years, advanced utilities have been augmenting their manual asset inspection programs with a data-rich approach. For example, it is now possible to carry out single-flight consolidated linear inspections, using helicopter cameras and sensors to simultaneously capture HD video, LiDAR (3-D data) and hyperspectral image data for the full length of a transmission or distribution line.
Once this data has been captured, it can be stored for later use on the cloud, allowing for an inspector to carry out a “virtual” inspection at any time. Crucially, with shelter-in-place rules in effect, this can be done from anywhere with an internet connection, allowing power line inspectors to join the ranks of those who can work from home for the first time.
Of course, this does not entirely negate the need for physical inspections. However, it gives teams advanced situational awareness so that they can plan ahead based on intelligence of what they will come across—for example, will they need a truck capable of elevating them 40 feet in the air, or 100 feet?
What’s more, if this data is collected across the network (or a large portion of it), the utility benefits from a holistic asset condition assessment. This makes it possible to make better informed, more intelligent decisions on prioritizing areas and assets for inspection, thereby helping ensure they get the best use out of a capacity-constrained workforce.
Finally, the utility can then use the LiDAR data to create 3-D flight plans to carry out fully automated inspection activities using aerial drones. This increases the efficiency of inspection teams by reducing the ground they need to cover—useful at any time, doubly so at a time of reduced manpower.
Crises Collide
However, even if COVID-19 is proving a manageable problem as far as power line inspection and management is concerned, for many utilities it’s also a compounding factor for another potential crisis altogether: namely, wildfires.
In the Northern Hemisphere, we are approaching summer and peak wildfire season in areas such as California. In both 2018 and 2019 the state suffered devastating fires, and the problem is only expected to increase. In a recent global survey of utilities by Accenture, 73% of respondents said extreme weather represents a significant challenge to network operations and safety, and 92% expect extreme weather will increase over the next 10 years. Less than a quarter (24%) believe their businesses are well-prepared to handle it.
What’s more, 2020 looks set to be equally high-risk. According to the U.S. Drought Monitor, 58% of California was abnormally dry on April 23, compared to 6% on the same date in 2019—nearly 36% of the state suffering drought, particularly the North.
What does this mean in the context of COVID-19? The same personnel pressures and social distancing measures that have made power line inspection more difficult have had the same effect with preparations for wildfire season. Tasks such as vegetation management near power lines, replacing old utility poles, and clearing brush have been slowed. Planned setting of controlled small fires has been similarly reduced or even stopped— the U.S. Forest Service has suspended controlled burns and in-person training of firefighters.
Stay-at-home orders may have some mitigating effects on wildfire season. Richard Carr of the Canadian Forest Service, which also faces a significant wildfire threat, points out that reduced recreational use of forests may mean fewer human-caused blazes, which account for roughly half the fire starts in Canada. However, on balance, it seems clear that the wildfire threat is one compounded by the difficulties brought on by COVID-19, not eased by them.
Ultimately it cannot be predicted how long the virus will continue to hinder operations, whether there will be a second wave, or exactly how bad this year’s wildfire season will prove to be. The only option to utilities is to prepare as best as they can. Partly, this will entail adjusting processes and carefully managing workforces, but modern power line inspection technology can also be a powerful tool in helping utilities better understand their network and prioritize inspection programs.
—Paul Frey is chief operations officer for Sharper Shape, a global leader in unmanned aircraft systems inspections of electric utility lines and facilities.
The post Power Line Management in the Time of Coronavirus appeared first on POWER Magazine.