The post Self-Tuning Artificial Intelligence Improves Plant Efficiency and Flexibility appeared first on POWER Magazine.
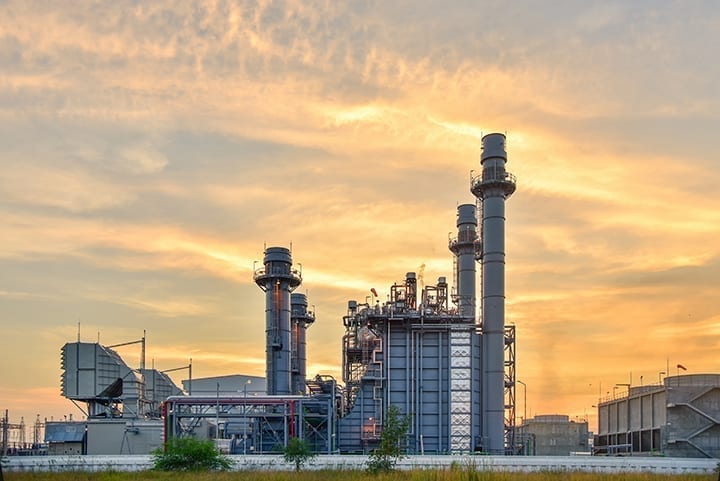
Flexible plant operations are highly desirable in today’s power generation industry. Every plant owner desires increased ramp rates and the ability to operate at lower loads so their plants will remain “in the money” longer in today’s competitive power markets. This goal, while laudable, remains elusive. The ADEX self-tuning artificial intelligence (AI) system allows plants to continuously optimize plant performance at any operating point rather than being constrained to a static “design point” commonly found in gas- and coal-fired plants. Better yet, no changes to the plant distributed control system (DCS) are required.
Renewable energy resources, coupled with internet technologies and emerging large-scale energy storage, fundamentally change the modern electricity markets. Wind and photovoltaic electricity resources have proved to be the most disruptive renewable energy technologies over the past few years and will continue to do so. The challenge for grid operators is managing these disparate electricity providers to match weather-dependent supply with consumers demanding more independence and flexibility to manage personal demand patterns. The solution is multi-layered. A new regulatory framework is needed to address accelerating market changes, and electricity generators must evolve their business models to remain competitive. Technology developers must provide regulators and generators with the necessary computer tools to ensure a reliable and efficient electricity supply system continues.
Not all electricity suppliers are equipped to compete in this new electricity marketplace, particularly those with significant coal-fired infrastructure. Initially designed to operate at baseload for months on end, coal plants are often disadvantaged in a competitive electricity market that values flexibility in plant operations, particularly in those regions with sizeable amounts of renewable resources. Cycling most coal plants adversely affect equipment life, the startup is time-consuming, and operation at load low for an extended period of continuous load-following operation is challenging. Gas-fired plants, principally combined cycle plants (CCPs), feel the competitive heat from increased grid-connected renewable energy resources placed higher in the dispatch order. The common need by conventional steam plants and more modern CCPs is a plant control system designed for more efficient and flexible operation.
What does “flexible operation” mean to the power plant owner? As with any competitive market, the plant that delivers electricity under any operating condition will be called upon more often than plants unable to respond to the modern grid’s dynamic load change characteristics. For example, flexible plant operations are usually stated in terms of its minimum continuous operating load, ramp rates, and fast startup when grid imbalances necessitate, while remaining in compliance with regulatory requirements. If a plant, coal or gas, cannot perform these three functions, then that plant is at a significant competitive disadvantage. Thus, regional system operators force thermal power plants to run under new operating conditions, much closer to their constraints and outside their stable zones, ruled by their control systems (Figure 1).
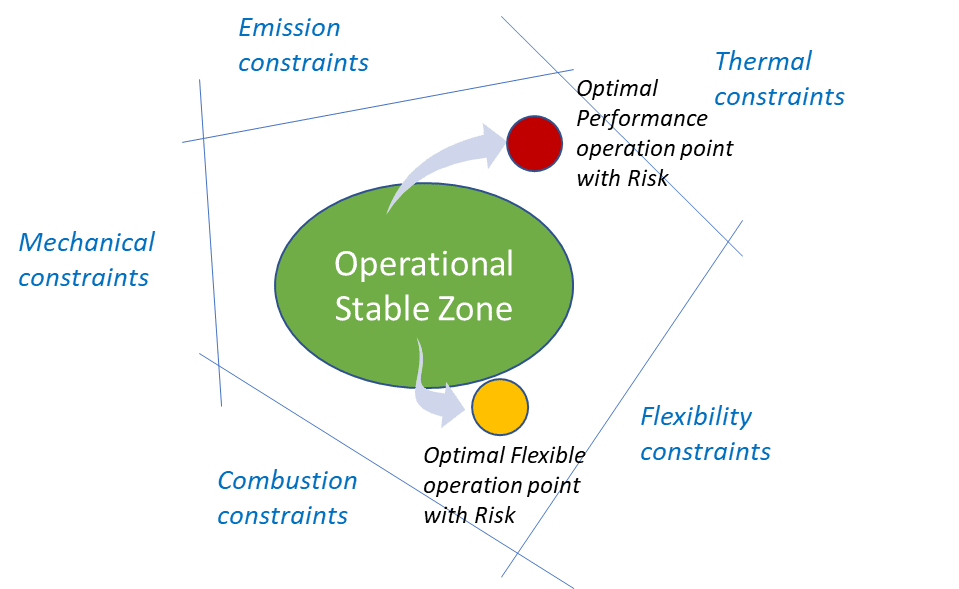
The Control Instability Problem
Thermal power plants under automatic control, like many other industrial plants, can suffer instability problems, particularly when power generation has to meet changes in demand. The main reason is that current automatic control systems are designed with fixed parameters, while the process dynamics are time-varying.
Power plants have several advanced process control (APC) systems available in the market based on various control methodologies, such as fuzzy logic, neural networks, or model predictive control. Each applies their control actions through well-known proportional-integral-derivative (PID) controllers at the DCS level, which interfaces with the plant’s actuators and sensors.
Each control methodology also shares a common paradigm: their parameters are set to control a model of the process, which were previously developed under defined operating conditions. However, when the time-varying process dynamics diverge from the model dynamics, the control system and the PID parameters become detuned, and the control performance can become unstable. When the control performance is erratic, flexible plant operations are limited, and dispatched hours are reduced.
Some facilities have turned to AI as a means to improve plant response. The drawback to AI is the lengthy period of “deep learning,” including “big data” collection under all possible operating scenarios before an AI controller can function independently. However, many of these technologies have proven to be more hype than hope, and the power industry has tested and rejected many AI-enabled solutions. The “control problem” now becomes correctly identifying the new dynamic relationship between control system input-output variables at all possible operating states, not just those that are predictable. For a modern steam plant, this is an impossible task.
Self-tuning AI: The ADEX Controller
Many electricity generators that are frustrated with their poor performance in a competitive marketplace may be surprised to learn that their plants are mechanically capable of greater operating flexibility, only to find that their plant controls are the limiting factor. If plant computing power or capability is not the issue, expensive hardware retrofits are also not the answer.
ADEX is a novel control technology that runs parallel with the plant DCS, not in the cloud. ADEX auto-adjusts its parameters in real-time to any of the infinite possible operating contexts and can guide process variables through desired trajectories, with no big data or machine learning systems. All this power relies on a new multivariable ADEX adaptive predictive controller that expands the stable process zone of operation (Figure 2) to include new challenging optimal scenarios.
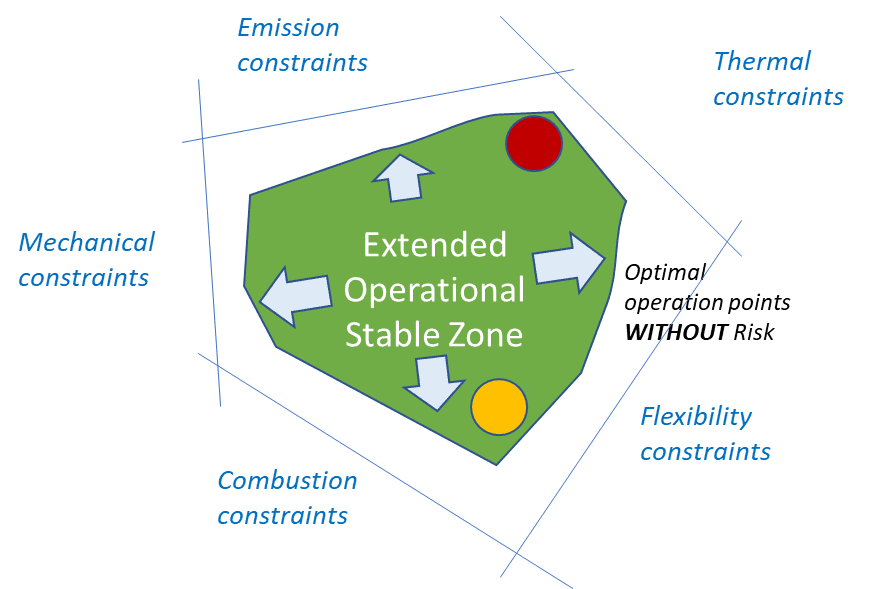
An overview of how the ADEX controller accomplishes this impressive task is shown in the ADEX controller block diagram (Figure 3).
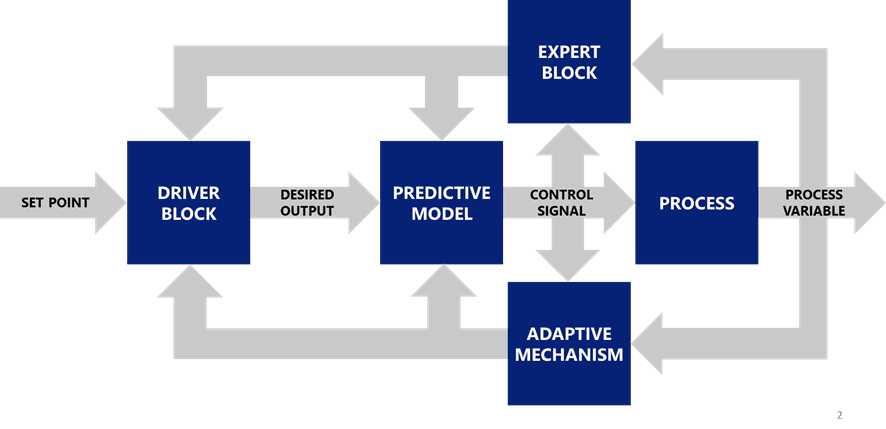
The methodological principles that govern ADEX controller operation and performance may be described in three parts.
1. Optimal Process Guidance describes the forward path of the ADEX controller block diagram that determines the controller operation (Figure 3). First, the process control signal is calculated by an adaptive predictive (AP) model to make the predicted process output equal to the desired output. Second, this desired output belongs to a future desired output trajectory produced by a Driver Block that goes from the actual process output to the setpoint. Finally, the Driver Block optimizes a process performance criterion that determines Optimal Process Guidance when there are no prediction errors.
2. Self-Tuning Artificial Intelligence (ST AI) is provided by an adaptive mechanism shown in the lower feedback path of Figure 3. From the process input-output data and the prediction error, it adjusts in real time the AP model parameters so that the square of the prediction error tends towards zero in the gradient direction. Thus, the process output trajectory will converge towards the desired output trajectory resulting in process stability and optimized control performance.
3. Expert Control is represented by the Expert Block on top of Figure 3. An ADEX controller is configured for different process operation domains based on the operator knowledge of process dynamics in these domains. The Expert Block introduces rules to make the controller configuration always the appropriate one for the current process domain of operation. Thus, prior operator knowledge on the process dynamics improves the closed-loop performance, robustness, and stability.
In sum, the ADEX implementation of AI based on this model does not require predefined operating points before it is implemented. It can adjust key operational variables by itself in real time to accommodate the application’s time-varying context.
Improving Plant Operating Flexibility
The ADEX ST AI system identifies in real time the time-varying process dynamics, which enables the process output variables under control to be on target within an extended operational stable zone, where the thermodynamical, mechanical, and other design features of the plant enable greater operating flexibility. The mismatch of current fixed-parameter control systems and PID controllers with the time-varying plant dynamics can cause instability, such as oscillations of the process output variables, which reduces the operational stable zone of the plant and restricts flexible operation that could be achieved otherwise. Thus, the limiting factor for greater flexibility is not the plant’s design capabilities, but the existing control system.
ADEX does not require replacing a plant’s control system, the addition of new I&C, nor “big data” or long-term machine learning processes. ADEX obtains its data through the plant local area network (LAN) and control network plus minimal DCS reprogramming. ADEX can be turned on or off by the control room operators at any time. Using the same inputs as the existing plant control system, the ADEX Controller determines a different behavior on the actuator that brings a different process performance and different results.
Figure 4 illustrates the ADEX controller’s performance when installed on the superheat control system of a conventional steam plant. The superheat (SH) steam temperature (green) is shown with its setpoint (red) during two hours of variable load operation. The left-side graph illustrates the existing APC’s performance when controlling the SH spray valve position (orange). The lack of anticipation and the PID reaction to the error allows the process to oscillate, with relevant peaks and drops of temperature. The right-side graph illustrates the performance of the ADEX system’s adaptive predictive technology when switched on. Note that a different behavior of the valve brings the SH steam temperature stabilization, even at minimum load. The following two case studies illustrate the application of the ADEX ST AI.
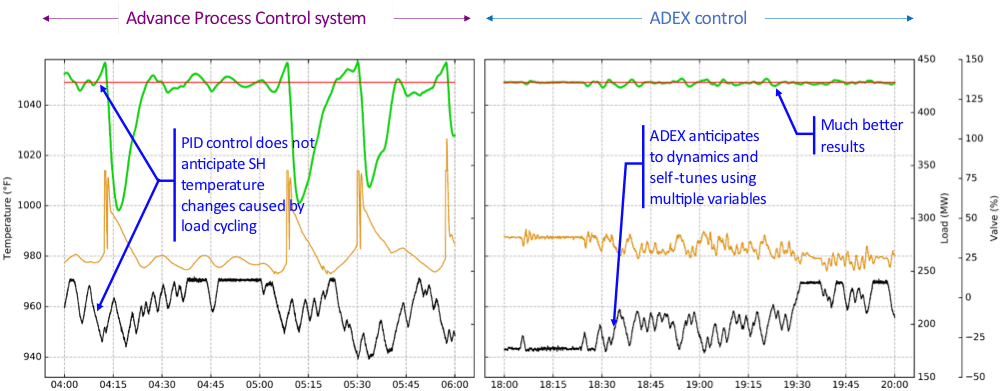
Case Study 1: Adding Operating Flexibility to a Coal-fired Power Plant
An ENEL three-unit 1.1-GW lignite-burning plant was struggling to deliver the load-following performance required by the system operator. Based on PID controllers, the existing control system produced unacceptable steam pressure and temperature oscillations, preventing the plant from accurately following the system operator’s required load profile (Figure 5). The top graph shows how the existing APC was limiting the ramp rate to 1.5 MW/minute due to the oscillations in SH steam pressure (grey) with a maximum amplitude of 237 psi (1.650 kPa) and SH steam temperature (green) of up to 30F (16.6C).
After ADEX ST AI was applied, the ramp rate doubled to 3 MW/minute as shown in the bottom graph of Figure 5. The load delivered (in black) followed dispatch orders (in red) 73% more accurately than before. Steam pressure and temperature excursions were eliminated, increasing the stability of both processes by 45% and 47%, respectively. Thermal stress on the steam generator was significantly reduced, and its capability to cycle was enhanced. The time from minimum load to full load on the plant was halved from 3.5 hours to 1 hour 45 minutes. This performance improvement allowed the plant to be dispatched more often in a load-following mode.
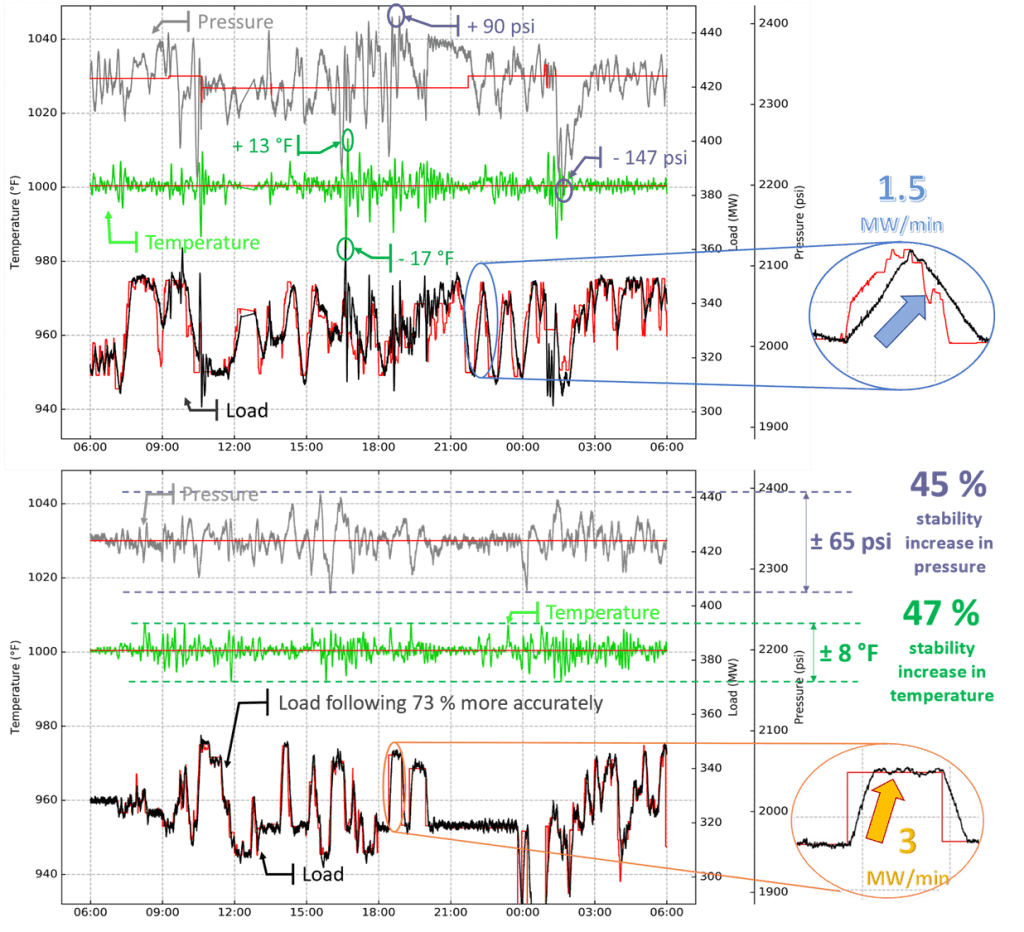
Case Study 2: Boosting the Efficiency of a Combined Cycle Plant
The 786-MW Amorebieta 2×1 CCP, located in the north of Spain, is owned by Bizkaia Energia. The plant uses two General Electric MS9001 GA DLN 2.0+ combustion turbines (CTs) and an Alstom DKYZZ3-2N41 steam turbine. The plant operates in automatic generation control (AGC) mode, cycling more than 30% of load an average of 150 times per day. However, ramp rates and plant minimum load were limited by SH temperature excursions and subjected the plant to excessive thermal stress. The left-hand side of Figure 6 shows the plant has experienced peaks of +7C (+12.6F) and temperature drops of up to –30C (–54F) in SH steam temperature during cycling operation.
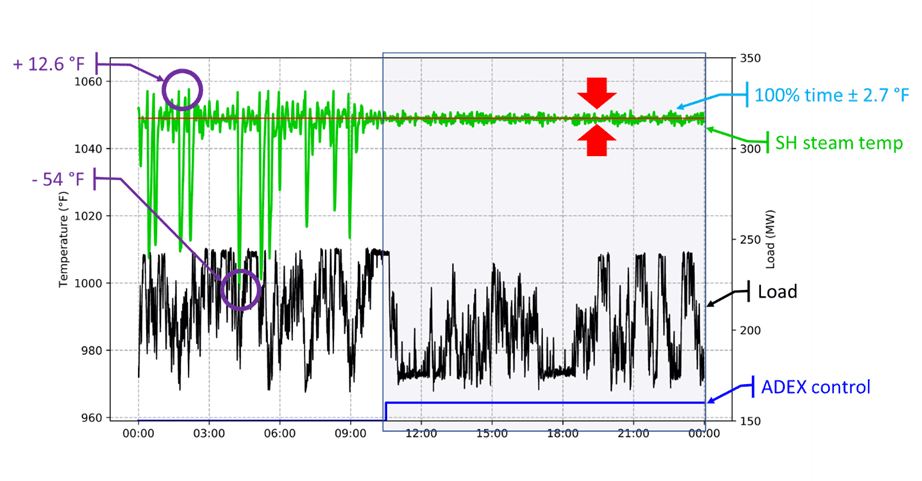
Bizkaia Energia developed a game plan to enhance the plant’s dispatchability by increasing the plant’s ramp rate and reducing its minimum load capability by successfully controlling the SH temperature oscillations. The right-hand side of Figure 6 shows how, since ADEX Self-tuning AI was applied, SH temperatures have maintained ±1.5C (±2.7F) around the setpoint 100% of the time, even under constant cycling operation.
With steam temperature excursions eliminated, the average steam temperature at the turbine inlet was raised by 4.8C (8.64F), which resulted in a heat rate improvement of 0.12%. The stability provided by ADEX optimizers also allowed an increase in the steam temperature setpoint of 2.1C (3.78F) for an additional heat rate improvement of 0.05%. Further, close control of SH temperature has reduced the induced thermal stress on the plant’s superheater headers, increasing component life expectancy and plant availability.
Additionally, the plant has enhanced its dispatchability by increasing its ramp rate from 15 MW/minute to 24 MW/minute (a 60% improvement), and reducing minimum plant load from 270 MW to 205 MW (24%) in 1×1 operation. Ramp rate improvement will also be reflected in the plant’s increased dispatch rate, particularly under AGC. The left-hand side of Figure 7 illustrates superheated steam temperature excursions that occurred during load changes under the previous plant control system operation. The right-hand side graph shows the operation of the plant after the ADEX optimizer was installed. The result was an increase in plant capacity delivered under AGC with SH temperature under close control.
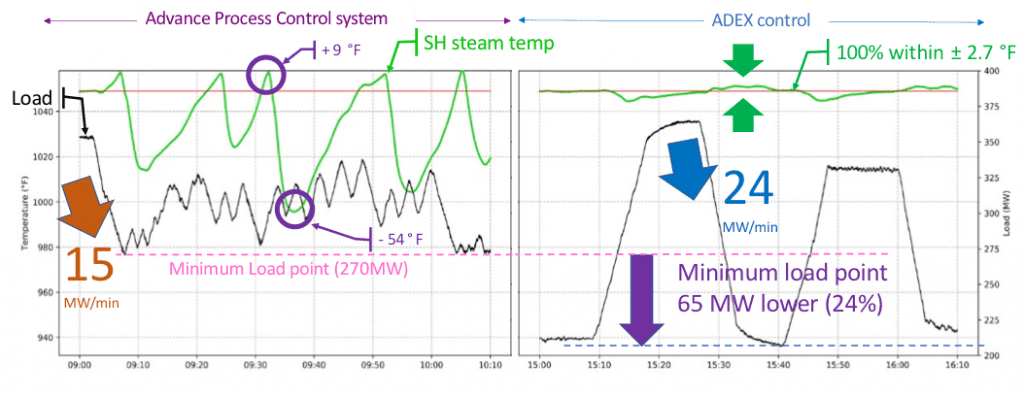
Those higher ramp rates and lower minimum loads produced more demanding combustion conditions in the CTs too, affecting flame stability, NOx formation, and combustion dynamics. The ADEX Self-tuning AI enabled the solution of those problems at Bizkaia Energia through the optimization of the fuel gas heaters, controlling the gas temperature five times more accurately than previously, following the Wobbe Index setpoint and meeting the demanding performance conditions imposed by flexible plant operations.
Conclusions
The ADEX Self-tuning AI allows under-performing plants to improve their thermal efficiency while minimizing thermal stress to the equipment, reduce startup time, and improve operating flexibility for both coal-fired and combined cycle plants. Flexible plants, particularly responsive plants with excellent ramp rates, high turn-down, and good load-following capabilities under AGC, are particularly valuable to a system operator. Also, the plant moves up in the dispatch order, which produces a greater economic return on the owner’s plant investment.
—Jose Martinez is CEO of ADEX Group, Isaias Martin-Hoyo is COO of ADEX USA, and Ravi Krishnan is managing director of Krishnan & Associates. This article was written for ADEX in cooperation with Krishnan & Associates, a specialized energy industry marketing firm.
The post Self-Tuning Artificial Intelligence Improves Plant Efficiency and Flexibility appeared first on POWER Magazine.