The post The POWER Interview: Cleaning Up a Radiologically Contaminated Site appeared first on POWER Magazine.
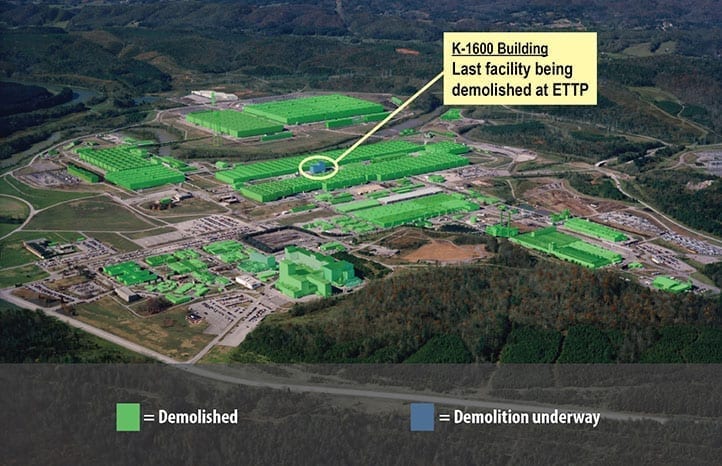
In the 1940s, the Oak Ridge Gaseous Diffusion Plant was built in unprecedented secrecy as part of the Manhattan Project. Its purpose was to provide enriched uranium for the world’s first atomic bomb, and it expanded operations during the Cold War, producing enriched uranium for defense and commercial purposes.
Uranium enrichment operations were halted at the site in 1985, and the plant was officially closed in 1987. UCOR, an Amentum-led partnership with Jacobs, has been the prime cleanup contractor at the site since 2011. POWER interviewed Kenneth Rueter, president and CEO of UCOR, to learn more about the work that has taken place at the site and how lessons learned could apply to nuclear power plant decommissioning projects.
POWER: The project was obviously extensive. Did the cleanup effort begin immediately and continue nonstop? If so, what were the most time-consuming aspects of the job? Was it expected to take this long to complete or were there unexpected delays along the way?
Rueter: In 1980, the Comprehensive Environmental Response, Compensation and Liability Act (CERCLA) became law, providing broad federal authority to address potential releases of hazardous substances.
In 1989, two years after the plant was closed at what is now known as the East Tennessee Technology Park (ETTP), the U.S. Department of Energy (DOE) established the Office of Environmental Management to oversee cleanup of hazardous materials at DOE facilities throughout the United States, including the Oak Ridge Reservation. After five decades of nuclear weapons production, the Cold War left 1.5 million cubic meters of solid waste and 88 million gallons of liquid waste across the DOE complex that required treatment and permanent safe storage. In addition to the decontamination of soil and groundwater at these sites, thousands of buildings and structures had to be decontaminated and decommissioned.
Also, in 1989, the Oak Ridge Reservation was placed on the National Priorities List, identifying it as a site to be cleaned up under the provisions of CERCLA. Remediation work began at that time with Lockheed Martin Energy Systems Inc. as the prime cleanup contractor. Bechtel Jacobs replaced Lockheed Martin in 1998, and then UCOR became DOE’s prime cleanup contractor for ETTP in 2011.
DOE realized from the beginning that cleanup of the former gaseous diffusion complex would be a multi-decade undertaking. Also, from the beginning the Department had as its vision transforming the site into a multi-use industrial park, transferring the land for industrial recruitment and job creation.
The most time-consuming elements of the project involved working in hazardous conditions among contaminated and dilapidated structures. Buildings scheduled for demolition were laced with radioactive materials. Years of unregulated waste disposal practices had polluted the soil and groundwater. Demolition of the site’s centerpiece—the mile-long K-25 gaseous diffusion building (Figure 1)—was the largest teardown ever undertaken in the DOE complex.
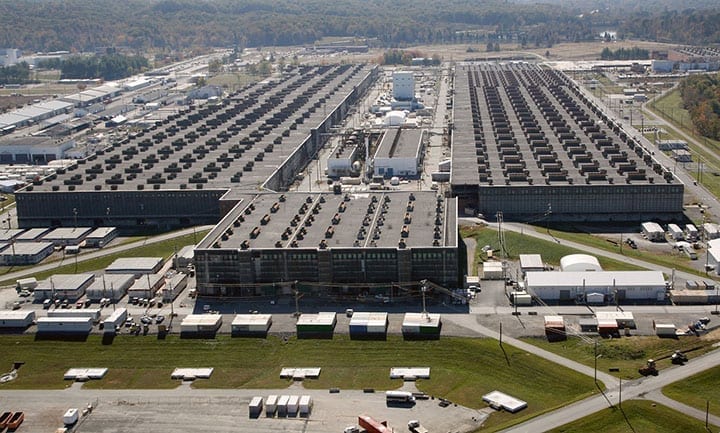
POWER: What best practices can you share, specifically concerning decontamination and environmental cleanup, that would benefit nuclear power plant decommissioning teams?
Rueter: It may not be obvious how decommissioning is applicable to power. For us, our ability to safely decommission nuclear facilities and dispose of waste without harm to the public or environment is directly related to the future of nuclear power generation in the United States and across the world. That is because the public and lawmakers need to have confidence that our industry has the ability to do that.
In many ways, UCOR has provided a model for commercial nuclear plant decommissioning in an even more hazardous environment. UCOR executes elaborate facility, equipment, component, soil, and groundwater characterization plans to provide data required to create work plans. These plans contain extensive analyses designed to identify hazards and implement controls to protect workers and the environment. Project safety and operational personnel work with suppliers to design, manufacture, and procure personal protective equipment and other equipment required to support work in extreme conditions. Innovative approaches that reduce or eliminate the need for human entrance into potentially hazardous environments are also employed.
As a learning organization, UCOR uses a timely and transparent communications approach used to inform employees and subcontractors about the various hazards that may be encountered as well as the mitigations and corrective measures taken or planned to eliminate those hazards. Through our shared governance approach, workforce participation is expected and encouraged throughout the work planning as well as after the work is performed to ensure lessons learned are captured and implemented for future activities.
As a DOE Voluntary Protection Program (VPP) Star site, UCOR embraces a Zero Accident philosophy dedicated to the concept that all accidents are preventable.
POWER: Can you recount any specific challenges the project team faced and how they were overcome?
Rueter: There were many specific challenges over the decades, but four capture the main obstacles faced in D&D [deactivation and demolition] of this massive gaseous diffusion complex.
The first challenge was timing. The K-25 Building—the cornerstone of the five-plant process—was shut down in 1964, but decommissioning activities did not begin until 2002. The time span that elapsed—some 38 years—took its toll on the structure. General failure of the roof allowed significant water intrusion that continued throughout deactivation. This affected the general working environment with falling and standing water compounded by the mold growth that would make respiratory protection mandatory for building entry.
The condition of the building made in nearly impossible to work in some areas, so the facility had to be determined to be criticality incredible before it could be demolished. This required extensive characterization efforts to find uranium deposits that were left in the process piping because the facility was not shut down correctly and the process piping was not purged as it should have been.
Second, the sheer size of the gaseous diffusion facilities presented unique challenges, not only with the demolition and waste hauling aspects of the job, but particularly with deactivation activities. Due to the repetitive nature of the process, identical deactivation activities were often done literally thousands of times. Whether it was separating compressors from their motors, cutting and capping converters, myriad other deactivation activities, these tasks occurred thousands of times. Analyzing repetitive tasks is usually associated with manufacturing processes not D&D. In most cases, D&D is anything but repetitive. In the case of the gaseous diffusion facilities, repetition was, in fact, the predominant feature. Process improvements proved crucial in holding cost and accelerating schedules.
Often, process improvement teams would analyze a series of tasks and find ways to improve efficiency, saving an hour or two per activity set. While this may not seem significant, if that activity set is repeated 6,000 times, it results in a savings of three to six work-years.
The third challenge was waste volumes. Once demolition commenced, it becomes readily apparent that efficient waste disposition is paramount. Fortunately, Oak Ridge has an on-site disposal cell and, even more fortuitously, a haul road that extends seven miles from the K-25 site to the Environmental Waste Management Facility (EMWMF) near the Y-12 National Security Complex. To streamline the process, we developed an innovative RFID [radio frequency identification] system to help track and manage the trucks as well as the waste data so that it was accurately captured and controlled. We also used a “pack-as-you-go” approach to waste management, which prevented contaminated waste material from piling up and causing increased hazard to workers and the environment.
The fourth challenge was Technicium-99 [Tc-99]. Tc-99 is a low-energy beta emitter that is soluble in water. Some gaseous diffusion equipment and parts of the building structures themselves were contaminated with Tc-99. Approximately 88% of the overall volume of Tc-99 waste was able to be disposed of on-site at EMWMF. UCOR also oversaw design of [a] reusable container that would accommodate large compressors. This innovation saved the K-25 project over $ 1 million.
POWER: Were there any positive surprises during the project, such as tasks that were completed more easily than expected?
Rueter: Except for the availability of onsite waste disposal via a dedicated haul road, we would be hard-pressed to identify “positive surprises” that made project completion easier than expected.
Through planning and allocation of resources, UCOR was able to complete the cleanup (Figure 2) of ETTP four years ahead of DOE’s schedule at a savings to taxpayers of approximately $ 80 million, while also avoiding $ 500 million of environmental liabilities.
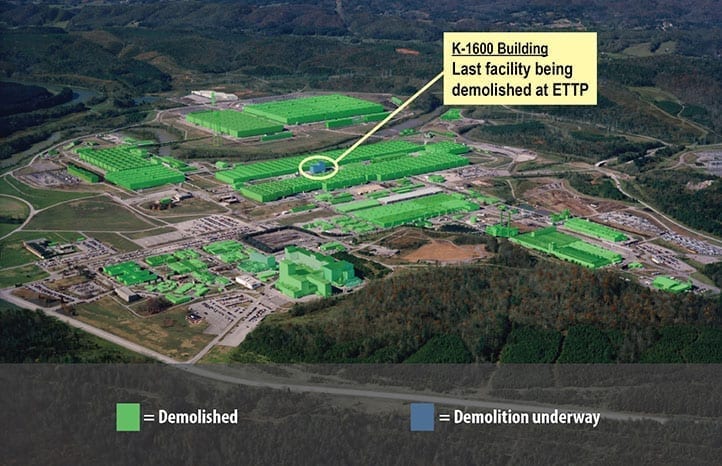
POWER: How many workers were regularly involved in the project? What expertise was vitally important to success?
Rueter: Unquestionably, the workforce is the key to our success. Once assembled, the skills and talents of these workers form a unique team of diverse backgrounds and disciplines that, if disbanded, would be difficult to duplicate. Blended together and properly applied and managed, the current team creates an unparalleled force channeled toward achievement of goals and visions that serve vital national interests and set the stage for more cleanup progress in the decades ahead.
The UCOR workforce has grown by 45% since inception of its contract in 2011. UCOR has approximately 1,800 employees dedicated to its Oak Ridge mission, up from 1,248 in 2011. During the same period, Congressional funding grew from $ 420 million to $ 646 million annually.
The UCOR workforce is a specialized team of professionals, ranging from engineers and accountants to millwrights, carpenters, electricians, chemical operators, riggers, equipment operators, waste management specialists, and more. Many of those come through the North America’s Building Trades Unions and the Atomic Trades and Labor Council. All were vital to the success of this project.
POWER: Is there anything else you’d like to share about the project?
Rueter: UCOR has a rich history of finishing projects ahead of schedule and under budget, thereby accelerating cleanup by years. Through 2020 to date, UCOR’s highly skilled workforce has accomplished the following:
- Disposition of more than 31 million cubic feet of hazardous, radiological, and sanitary waste.
- Demolition of more than 6.1 million square feet of facilities.
- Management/treatment of more than 820 million gallons of low-level wastewater.
- Transportation of 104,182 loads of waste over 6.8 million safe miles.
- Removal, transportation, and disposal of 7,104 loads (9,412 cubic yards) of asbestos-containing materials.
- Transfer of 1,300 acres of government land for redevelopment/reuse by private sector.
We have an exemplary safety record. In 2019, UCOR was named one of America’s Safest Companies by EHS Today magazine, recognizing its best-in-class practices that go beyond compliance with regulatory requirements. Also, we have twice been awarded DOE’s VPP Star Status, which is the highest acknowledgement of a safety culture that the Department awards. That award was made in 2015 and recertified in 2019.
While never losing focus of its mission, UCOR has heavily invested time, money, and volunteer hours into the community. A key focus has been development of the future workforce. As one example, in 2016, UCOR led the creation of a new Nuclear Decommissioning & Environmental Management minor at the University of Tennessee for its Nuclear Engineering Department—the first of its kind in the United States.
The cleanup completion will reduce risk to workers, the public, and the environment, while enabling cleanup resources to continue to transition to the east portion of the Oak Ridge Reservation—Oak Ridge National Laboratory and the Y-12 National Security Complex. It will also leave behind a thriving multi-use industrial park, national park, and conservation area.
—Aaron Larson is POWER’s executive editor (@AaronL_Power, @POWERmagazine).
The post The POWER Interview: Cleaning Up a Radiologically Contaminated Site appeared first on POWER Magazine.