The post How Much Will Hydrogen-Based Power Cost? appeared first on POWER Magazine.
Costs associated with 40 hydrogen technologies used in 35 applications, including for heat and power, could tumble dramatically over the next decade as the scale-up of hydrogen production, distribution, and equipment and component manufacturing continues. For some applications, hydrogen could become competitive with other low-carbon alternatives, and even conventional options. Those are key findings from an in-depth assessment of industry-provided hydrogen application costs that the Hydrogen Council—an international CEO-level advisory body—underscored in a Jan. 20–released report.
The findings offer an important glimpse at growing efforts to integrate hydrogen into the global energy framework. As part of concerted decarbonization goals, 18 governments (whose economies account for 70% of global gross domestic product) had developed detailed strategies for deploying hydrogen solutions, as of January. Industry, too, is paying attention to sharp improvements to cost drivers associated with “renewable” hydrogen production, and the versatile role hydrogen could play in future energy systems.
The Hydrogen Council, which serves as a point of collaboration for the hydrogen industry (but also a resource for safety standards and an interlocutor for the investment community), for example, noted its membership has surged from 13 companies in 2017 to 81 companies as of mid-January. “Core” power-sector members include CEOs from EDF, ENGIE, Equinor, Shell, Total, Siemens, and Cummins, and “supporting” members include ITOCHU Corp., Marubeni, and Mitsubishi Heavy Industries. In 2020, the council also launched a new investor group, a membership category that currently comprises five European banks.
While the council actively promotes hydrogen as a critical component of future global industrial decarbonization, it admits that despite increased interest—and more than 30 major investments in segments such as heavy-duty trucking, rail, and steel production from low-carbon or renewable hydrogen—new projects have not yet been sanctioned. The group says this is “likely due to the lack of suitable policy and regulatory frameworks,” and, significantly, a lack of visibility on near-term and long-term economic viability and industry readiness. It suggests governments can boost the “hydrogen economy” with increased coordination, standardization, and by focusing on infrastructure investments, as well as providing incentives.
Industry’s role, meanwhile, focuses on establishing a market. That could be achieved by reducing market uncertainty, focusing on scaling applications, and advancing technologies that create the biggest “improvement for investment.” For example, “scaling fuel cell production from 10,000 to 200,000 units can reduce unit costs by as much as 45%, irrespective of any major technological breakthroughs, and can impact multiple end-use cases. Scaling up to 70 GW of electrolysis will lead to electrolyser costs of less than $ 400 per kW,” it claims.
That’s why the council put out its report, “Path to Hydrogen Competitiveness: A Cost Perspective.” The report, which was reviewed by an independent advisory group, comprising hydrogen and energy transition experts, stems from McKinsey & Co.’s efforts to collect and analyze 25,000 data points from 30 companies across the full hydrogen value chain in the U.S., Europe, Japan, South Korea, and China. It broke it down to 35 applications, which span from transport—to include fuel cell trains and forklifts, aviation, and ships—to industry feedstock, and heat and power. It further breaks down hydrogen heat and power by applications for buildings, and for industry and the grid. For each application, it assessed the total cost of ownership (TOC) for a “low-carbon hydrogen solution” from 2020 to 2050, and then compared the costs with other low-carbon solutions, such as batteries, vehicles, and heat pumps, as well as conventional technologies, such as diesel-powered vehicles and gas boilers (Figure 1). It says more than 70% of the TOC it surveyed were for non-transport applications.
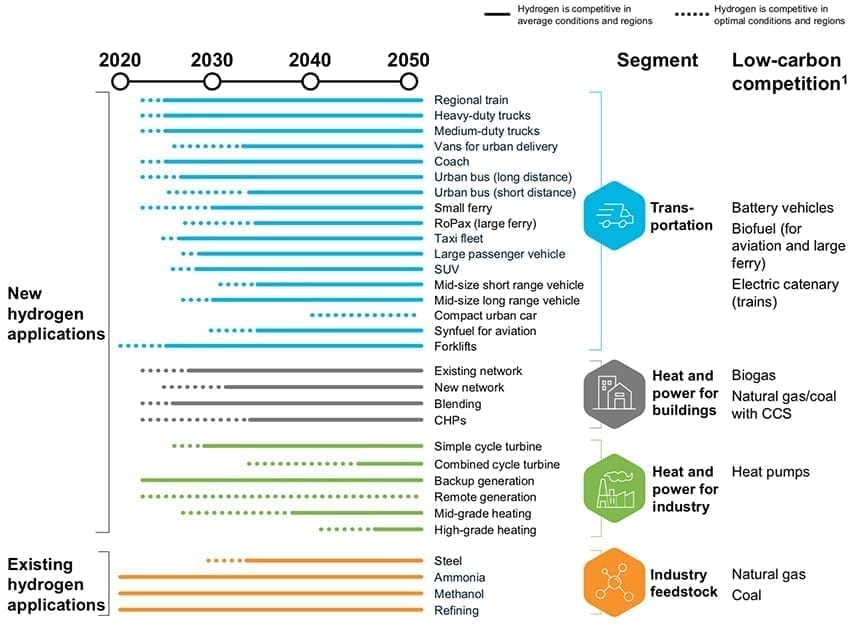
Among its major findings is that, while it depends greatly on the region, for power applications, the eventual costs of renewable hydrogen matters. Today, renewable hydrogen from electrolysis costs about $ 6/kilogram (kg). Generally, however, it concludes that in the short-term (through 2025), hydrogen could become competitive in transportation, mostly for large vehicles with long ranges—trains and coaches, for example—and forklifts. By 2030, if costs of hydrogen production and distribution continue to fall, hydrogen solutions could compete with other low-carbon alternatives in simple cycle hydrogen turbines for peak power, hydrogen boilers, and industry heating. Some specific power applications detailed in the report follow.
Fuel Cells for Combined Heat and Power (FC-CHP). In this application, hydrogen is used to generate power from fuel cells, and then it recovers and uses the by-product heat for hot water, space heating, or cooling in residential and commercial buildings. Compared to both low-carbon (hydrogen boilers and heat pumps with grid electricity) and natural gas (boiler plus grid electricity and natural gas CHP), FC-CHP may prove to be a viable alternative for a house in North England by 2030, when the cost of hydrogen is about $ 1.9/kg.
Industrial Heat. Electrification will continue to be the lowest-cost decarbonization option for low-grade heat—so hydrogen won’t likely play a significant role. For mid- and high-grade heat, biomass is an option, but it faces supply constraints, and CCS will likely be constrained to regions with access to carbon dioxide storage. Where those are not options, hydrogen and electric heating will be the only low-carbon solutions, the report says.
Generators. While backup generators primarily use diesel or natural gas, hydrogen fuel cell generators may be viable alternatives, especially in remote locations where batteries and renewables are unviable due to sub-optimal conditions. For instance, the hydrogen alternative could save more than 40% compared to a solar plant and battery in Edinburgh. Still, it notes, a hydrogen cost of $ 6/kg delivered to a very remote location is required to breakeven, “which may be challenging to achieve.”
In southern Spain, meanwhile, a hydrogen fuel generator would be 30% more expensive than a solar-battery hybrid in 2030. Currently, the two main factors influencing the cost of hydrogen generators are the cost of the fuel cell and tank system, and the cost of hydrogen production and distribution. Estimates suggest the cost of fuel cells and hydrogen tanks is set to decline by 70% by 2030, driven by larger market volumes of fuel cells and tanks across several applications, such as with transportation. Meanwhile, the cost of hydrogen supplied is projected to decline by about 20% to 40% by 2030, making it possible for hydrogen to be dispensed between $ 4.50/kg and $ 6/kg.
Turbines for Grid Power Generation. Systems that use hydrogen as fuel for power generation must provide flexible energy to ensure stability and resilience. So far, several power-to-gas systems, which entail the conversion of renewable energy to gaseous energy carriers via electrolysis, exist, but many remain small in scale—less than 1 MW. However, several large “renewable hydrogen” projects have been proposed. In tandem, since 2010, the cost of electrolysis has fallen about 60% (from between $ 10/kg and $ 15/kg hydrogen to as low as $ 4/kg), the report says. One example it cites that involves offshore wind–based electrolysis in Germany suggests that by 2030 costs could fall another 60%. Meanwhile, hydrogen has also already been combusted in gas turbines, albeit at low volumes, and with so-called “grey hydrogen,” which comes from fossil fuels. However, all major gas turbine manufacturers are currently developing gas turbines that could combust 100% hydrogen, both for peaking and baseload power applications as a decarbonized alternative to natural gas.
But according to the report, low-carbon baseload supply hydrogen will only be “relevant in regions constrained in renewables potential and situations where alternatives like fossil fuels with direct CCS or biomass (wood chips or biogas) are not an option.” In such cases, it notes, “companies could import hydrogen and use it to power hydrogen turbines.” For an assumed import price of $ 3/kg of hydrogen, power produced from hydrogen turbines could cost about $ 140/MWh. In comparison, Lazard’s November 2019 levelized cost of energy (LCOE) analysis suggests unsubsidized natural gas combined cycle generation today costs between $ 44/MWh and $ 68/MWh.
The economics for hydrogen gas turbines is better if units provide short-term multi-hour balancing (such as with a simple cycle peaking plant), or multi-day/week generation when paired with combined cycle generation at times when renewable generation is low. “In this way, hydrogen can act as a buffer and long-term storage option for the power system,” it says. Storage of large hydrogen volumes will be especially feasible at a low cost. Cavern-based storage—such as a project proposed by Mitsubishi Hitachi Power Systems in Utah—could reach about $ 0.30/kg of hydrogen—and that means, compared to batteries, its impact of storage time on overall cost is more limited. “Consequently, hydrogen should offer advantages over batteries, especially for longer storage durations of more than five hours up to days or even weeks,” it concludes.
However, a key drawback of this “power-to-gas-to-power” route, if electrolysis is used for hydrogen production, is the round-trip efficiency, which is “around 45%,” it says. The report provides an example to illustrate the cost penalty per MWh associated with the power-to-gas-to-power route: “Hydrogen generation from low-cost renewables at $ 25/MWh with a capacity factor of 50% yields a cost of $ 1.70/kg of hydrogen produced. Storing this hydrogen underground will add about another $ 0.30/kg, thus the hydrogen costs $ 2/kg. If this hydrogen is used to generate power, the resulting cost is $ 100 to $ 200/MWh. In ideal conditions (e.g. a CCGT turbine at 60% utilisation), the cost is $ 100/MWh, while simple-cycle turbines at 25% utilisation would deliver power at $ 200/MWh.”
Still, the report is optimistic. Because hydrogen production costs will drive up to 80% of total power generation costs (Figure 2), if the technical feasibility of a 100% hydrogen turbine is proven, the capital expense of hydrogen turbines could “rival that of natural gas turbines by 2030,” it says. For now, however, “companies should use hydrogen-based power for high-value flexible generation first, and two, hydrogen baseload power generation for deep decarbonisation in situations with constrained renewables potential will require strong policy support.”
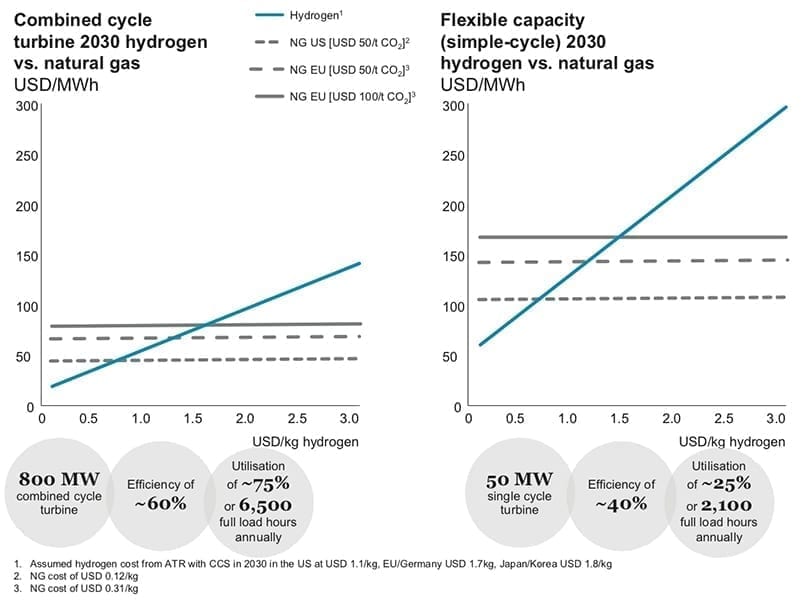
—Sonal Patel is a POWER senior associate editor.
The post How Much Will Hydrogen-Based Power Cost? appeared first on POWER Magazine.