The post Technology Triumph: Track 4A Is POWER’s Plant of the Year appeared first on POWER Magazine.
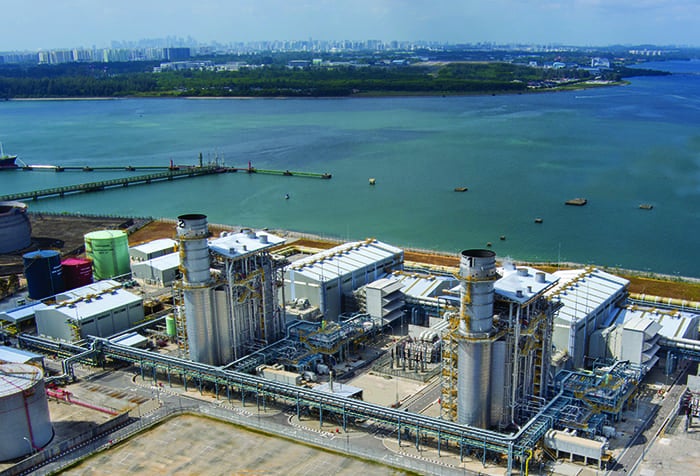
Winning POWER’s highest honor is Track 4A, Southern Power Generation’s 1.4-GW natural gas–fired power plant in southern Malaysia that is equipped with the first commercial GE 9HA.02 gas turbines—one of the world’s largest and most efficient power-generating models. Though jolted by the pandemic, an international team brought this first-of-a-kind plant online through innovative continuity efforts. The project is today a showcase of advanced technology integration and a meaningful model for balancing climate awareness, energy affordability, and reliability in power-hungry Southeast Asia.
Jim Vono, services general manager for GE Power’s Asia Pacific and South Asian division, recalled a poignant moment in mid-March 2020, mere days before Malaysia’s government instituted a partial lockdown as an early response to the deadly COVID-19 pandemic. It was as thousands of people around the world who were involved in the design, testing, and construction of the world’s first GE 9HA.02 gas turbine model awaited news of first fire at Unit 1 of the two-unit 1,440-MW Track 4A power plant in Pasir Gudang. The milestone had crested from a “collective success, when tracked from the project’s notice to proceed” in October 2017. “It was quite incredible,” said Vono. The 9HA.02 “is a massive, massive piece of equipment, and to see it leave the factory, all the complexity of moving that massive equipment to a port, put on a ship to get it to site, removing it, transporting it, and then placed on its foundation—and eventually see it all put together to create this amazing feat of engineering and physics,” he said. “It’s special.”
But for all the activity that led up to that tremendous accomplishment, in the weeks that followed it, the government handed down more movement control orders, abruptly slowing the project’s trajectory. However, the project ultimately achieved commercial operation for Unit 1 on Jan. 1, 2021, and Unit 2 on Feb. 19, 2021. Even if well behind initial operation dates of June 2020 for Unit 1 and August 2020 for Unit 2, it was a feat accomplished, having overcome unprecedented, potentially paralyzing challenges.
But Track 4A is also POWER’s 2021 Plant of the Year Award winner because the landmark $ 1.1 billion project showcases an array of first-of-their-kind equipment. It both delineates a marked advancement for gas turbine technology and integrates it into a larger state-of-the-art system that is equipped to address present and future hurdles anticipated within a rapidly changing power landscape. Today, while the plant ensures reliability of a power-hungry region, it also provides affordable power that caters to government-led climate change mitigation efforts.
As laudable is that the project was a marvel of collaboration between some of the world’s biggest firms, including the intercontinental partnership that built it, which comprised U.S.-based technology conglomerate GE and Taiwanese engineering, procurement, and construction (EPC) services giant CTCI Corp.
These aspects are more remarkable considering that the team, forced to partially manage crucial project phases remotely, kept all the workers safe. As the project owner’s engineer AFRY Malaysia Sdn Bhd underscored, though the pandemic jolted its schedule, the project began successful commercial operation in February 2021, following a chaotic 39 months for Unit 1 and 40 months for Unit 2. That’s a total of 10 million man-hours—with zero lost-time injuries.
Borne Out of Crisis
The award-winning project’s story began in 2014, when Malaysia’s Energy Commission (EC) awarded SIPP Energy, a private vehicle, a fast-track project tender—“Track 4A”—to build, by 2018, two 720-MW combined cycle gas turbine (CCGT) power plants in Pasir Gudang through its special purpose vehicle Southern Power Generation (SPG). At the time, Peninsular Malaysia was grappling with power disruptions, forcing Tenaga Nasional Berhad (TNB), Malaysia’s largest electrical utility and a private company that is wholly owned by the government, to repeatedly import power from Thailand and Singapore to stabilize the grid. The EC deemed Track 4A essential for Pasir Gudang, a mangrove-fringed city in the southernmost reach of mainland Asia in Peninsular Malaysia’s state of Johor, which has long shouldered the region’s industrial activity. Strategically located just across the narrow Johor strait from Singapore, the city functions as an important international port and services hub in Asia, bolstered by its palm oil, petrochemical, and IT industries.
TNB at first withdrew but then returned to the project in 2017 with the acquisition of a 51% share in SPG, citing approval from the EC, as well as expected “earnings accretive to TNB” upon Track 4A’s scheduled commercial operation date. TNB, notably, raised its share in SPG to 70% in September 2020.
As Rizal Nordin, managing director at SPG, told POWER in June, Track 4A’s commercial operation increased Peninsular Malaysia’s generating capacity to 25,962 MW. But it also helps the nation meet its climate ambitions, he said. In 2017, as project development ramped up, the country was working out its now-official nationally determined contribution (NDC) to the Paris Agreement to reduce the intensity of its carbon emissions by 45% compared to 2005 levels by 2030. The country has also set a 20% renewable target by 2025. However, the EC suggests 11.6 GW of plant retirements, mostly coal-fired plants, are expected by 2029, which means Peninsular Malaysia will need at least 9.3 GW of new power capacity by the end of 2030 to meet demand growth and maintain system reliability.
Today, both Track 4A plants are fully operated and maintained by REMACO, a subsidiary of TNB Power Generation that develops, operates, and maintains the latter’s portfolio of power generating units. Owner SPG supplies power to TNB through a 21-year power purchase agreement (PPA).
![]() |
1. This graphic illustrates the separate roles played by companies affiliated with the Track 4A project. Courtesy: Southern Power Generation (SPG) |
According to SPG, the option to build gas-fired generation was also bolstered by TNB’s long-term gas supply framework with Malaysia’s state-owned oil and gas firm Petronas. Meanwhile, TNB had also previously worked with GE on other plants. Another crucial decisive factor related to shaping the project—including choosing its technology and key contractors (Figure 1)—was rooted in a vision to operate an efficient and reliable plant through the next 20 years, said Norlida Binti A. Manaf, corporate and business support director at SPG.
“GE was pretty advanced in terms of this technology as compared with other providers,” while SPG was determined to secure state-of-the-art technology. That’s why developers went with the first-of-its-kind 9HA.02 technology, she explained. “Some people may say that’s a big risk,” but SPG chose “the best in the market,” both to provide the necessary flexibility required in the present market as well as accommodate dramatic shifts forecast for the global power landscape, she said.
An Award-Worthy Collaboration
Another significant factor that likely boosted GE’s prospects is that the U.S. company bid for the EPC contract as part of a strategic consortium with Taiwanese EPC service provider CTCI. As Anthony Hsu, project manager at CTCI Corp. explained to POWER, the two companies’ synergies had already been proven.
“CTCI and GE have worked closely on several power plant projects in the Asia-Pacific region. We built an extensive track record of delivering and commissioning leading projects, including nuclear, thermal, cogeneration, and combined cycle power plants,” Hsu said. “Combining our strengths in project management, engineering, and construction management with GE’s cutting-edge machines, we have established a competitive EPC partnership.”
Under the EPC contract, for which the companies received a notice to proceed in October 2017, CTCI spearheaded project management, engineering, and procurement of balance of plant (BOP); overall construction management; and BOP commissioning works, Hsu said.
![]() |
AFRY Malaysia, part of AFRY Group—an international engineering, design and advisory company, formerly known as Pöyry Energy—meanwhile, served as the owner’s engineer, undertaking “project management and all duties and responsibilities expected from an experienced and skilled consultant for the EPC works,” the company told POWER. It also conducted the detailed engineering review, construction supervision, and commissioning assistance for the plant and interconnecting facility to meet contractual requirements for SPG’s role in the EPC contract and PPA.
First-of-Their-Kind Components
GE, meanwhile, served as the main equipment provider for the plant’s two single-shaft generating blocks. Each block is equipped with a world-first 9HA.02 gas turbine (see sidebar “A Long History of Advancements”) and an STF-D650 steam turbine, driving a W88-50WT25E-138 generator.
A Long History of AdvancementsSince General Electric (GE) launched its inaugural gas turbine—a 3.5-MW unit at the Belle Isle Station in Oklahoma City—in 1949, the original equipment manufacturer has marked a series of breakthroughs in gas turbine technology advancement to cater to changing markets. In 1967, in the aftermath of the Great Northeast Blackout, it installed its first combined-cycle plant. In the 1970s, it began developing and testing dry low-NOx (DLN) combustion systems, efforts that it has continuously re-innovated and streamlined to arrive at the state-of-the-art DLN 2.6e combustor with axial fuel staging that is incorporated into the 9HA.02 (Figure 2). In 2003, it heralded the start of the H-class era when it unveiled its 9H model. And in 2014, representing a step-change for its heavy-duty–class portfolio’s efficiency, it introduced two new air-cooled H-class turbines, the 9HA (50 Hz) and 7HA (60 Hz), which it said were developed through advancements in materials, aerodynamics, and advanced manufacturing.
In 2016, it deployed the first 397-MW 9HA.01 gas turbine with an efficiency of 62.22% at EDF’s Bouchain plant in France, and then a 7HA.01 at Chubu Electric’s Nishi Nagoya plant, with a 63.08% gross efficiency, in 2017. Also, in 2017, GE began commercial operation of the first 7HA.02 models at Exelon’s Wolf Hollow and Colorado Bend projects in Texas. But GE’s 9HA.02, launched at Track 4A, is the largest, “most efficient and advanced gas turbine in the 50-Hz market,” said Amit Kulkarni, senior executive, general manager, and head of GE’s Large Block Utility Product Management business. The 9HA.02, rated at 575 MW under ISO conditions, pushes net efficiency “beyond 64% combined cycle efficiency,” and boosts GE’s efforts to reach 65% by the early 2020s, he said. However, the 9HA.02’s commercial demonstration will soon be followed by the 7HA.03, a 60-Hz machine that will have a single-cycle net output of 430 MW, a remarkable 10-minute start-up, and a ramp rate of 75 MW per minute. The first two 7HA.03 units are under construction at Florida Power and Light’s Dania Beach Clean Energy Center. They are slated to begin operation in 2022. [For more, see POWER‘s feature: “A Brief History of GE Gas Turbines.”] |
As Amit Kulkarni, senior executive, general manager, and head of GE’s Large Block Utility Product Management business, told POWER, the 9HA.02 integrates advances in additive manufacturing and combustion breakthroughs in its 16 combustors, some previously showcased in the 7HA.01 and 7HA.02, like its DLN (dry low-NOx) 2.6e combustor with axial fuel staging (AFS), which enables lower nitrogen oxide emissions with improved turndown. However, the 9HA.02 uniquely incorporates an evolutionary improvement to the premixing fuel nozzles, a technology GE developed in collaboration with the U.S. Department of Energy to “deliver a step-change improvement in performance, emissions, and fuel flexibility,” Kulkarni said. The advanced DLN features also provide a “wider operability range,” he said. “We can go to better combustion dynamics, and because of that, the technology allows us to go to up to 50% hydrogen blends.” That’s significant for GE, which recently took a concerted step to position itself as a decarbonization leader, Kulkarni noted. For now, however, if the Track 4A turbines burn an alternative fuel, it will be distillate fuel oil, SPG told POWER.
According to GE, the 9HA.02’s efficiency boosts are also supported by its four-stage design, which incorporates a 3D aerodynamic hot gas path. For one, it features a titanium R1 blade row, which GE introduced in the 7HA.02. “It’s a larger blade, more airflow, greater output, and more importantly, greater hot-day output in a place like Malaysia or parts of Southeast Asia, where the temperatures are much higher,” he said. Hot-day output, Kulkarni noted, is a “critical” performance parameter in Asian markets owing to their unique climate conditions.
![]() |
3. For the first time in a GE H-class plant, Track 4A features a GE horizontal once-through (OT) heat recovery steam generator (HRSG) to capture exhaust heat from the gas turbine that would otherwise escape through the exhaust stack. While GE’s horizontal OT HRSG has the same basic arrangement as a horizontal drum HRSG, GE’s most popular HRSG type, it eliminates the high-pressure drum, thereby avoiding continuous blowdown. OT technology, which was validated at a 50-MW HRSG test facility in Switzerland in 2015, can also vary feedwater flow, helping to boost flexibility, efficiency, and daily cycling capabilities. Courtesy: GE |
As noteworthy is that for the first time installed in an H-class plant, Track 4A showcases a GE horizontal once-through heat recovery steam generator (HRSG, Figure 3). Because the plant is 12 miles away from Seletar International Airport, new rules promulgated during construction required the project team to revise the HRSG’s stack height to 56 meters from its designed 65 meters, said SPG’s Norlida.
One reason teams were able to adapt to the change so quickly is because “the architecture is very much modular, which allows for quicker inspection and maintenance activities that go along with the services contract” while also allowing a plant to go into commercial operations “at a much faster rate,” said Kulkarni.
The plant is controlled by GE’s Mark VIe integrated plant control system, an ethernet-based system equipped with intelligent controllers, input-output modules, secure cloud connectivity solutions, advanced analytics software, and apps to provide real-time process optimization and control of the plant’s complex processes. As part of its contract with SPG, GE also inked a 21-year services contract that includes GE Digital’s Predix Asset Performance Management solutions software to improve asset visibility, reliability, and availability, as well as also reducing maintenance and operating costs. In addition, data collected from sensors throughout the facility will be monitored and analyzed 24/7 at GE’s Monitoring & Diagnostics (M&D) Center in Kuala Lumpur.
Video: The story behind Track 4A and GE’s first 9HA.02. Courtesy: GE Power
Addressing Unprecedented Challenges
As SPG’s Norlida underscored, the company’s choice of contractors fit the bill as far as experience was concerned, but combined, the companies also offered the right measure of innovative problem-solving necessary to bring the first-of-its-kind plant online. Communication was crucial. Norlida’s own team, notably, comprises highly talented multi-skilled industry experts—most who are younger than 40. “I’m very passionate about my people,” she said. “And we motivate them to keep their mind open and encourage them” to express their ideas, she said.
![]() |
4. A worker onsite at the Track 4A power plant. Courtesy: GE |
CTCI’s Hsu also pointed to a diversity of expertise as a key project benefit. “The new 9HA.02 was built with the most advanced technology that comes with the most efficient output. The ancillary equipment was built with modularized design for transportation and site installation,” he noted. “We faced certain installation issue during the construction period, but it was solved promptly by the expert of GE and remote support. There were numerous technical advisors dispatched from each aspect to assist the installation and testing the works to ensure the work go smoothly.”
The solid collaboration and vast expertise proved especially crucial when the pandemic disrupted all planning. “Imagine how many people are onsite between us and our partners CTCI and the FieldCore team,” said Vono. “All of a sudden COVID comes into play. We had to work within these confines of keeping the people safe from the traditional perspective but then keeping the people safe from the COVID perspective.” GE, FieldCore, CTCI, and TNB “worked really hand-in-hand to try to minimize any risks that we had as the government was handing down movement control orders,” he said.
“We didn’t have a playbook for something as unprecedented as the COVID pandemic between us, so we had to develop certain things on the go,” Vono said. Efforts involved “collectively” digesting new government movement control orders to come up with a strategy” for how to navigate new constraints. Eventually, however, when cases were identified onsite, the project team was forced to demobilize.
“Demobilizing meant that in this case, almost everybody was leaving the plant,” Vono noted. “But you can’t just pick up and go home. You have to have a real strategy around how you ensure the plant and equipment that you leave behind will be preserved appropriately and ready for when you return.”
Compounding the issue was that the team didn’t know when it would be safe to return. Ultimately, the team decided to leave specialists behind to “maintain our preservation requirements” on certain equipment, he said.
AFRY, too, noted, the pandemic posed a “serious challenge” during the commissioning phase, because it “required specific skills, from the technical advisors to be deployed to the site.” Challenges were “successfully overcome by the goodwill of the Malaysian government and other involved governments of foreign countries playing a part in the project, by permitting essential technical personnel to travel, who of course ensured that all COVID-19 restrictions were followed,” it said. “The personnel could perform critical work required at the site to make the project a success despite the strict requirement of adhering to all applicable Standard Operating Procedures (SOP) due to the global pandemic.”
For Vono, if there was a glimmer to be found during the pandemic, it was that GE and its partners found a way to work digitally and remotely—“to connect all the people that we had to without actually being at site.” Before the pandemic, GE would “fly in all the subject matter experts (SME’s) that helped design” the turbine model so they could “support validations of NPIs [new product introductions], optimize controls, support first time commissioning activities and other systems assessments.” Lockdowns all over the world pushed the company to depend on live visualization and online collaboration, he said.
That added crucial time to simple tasks, he said. “What used to take three hours maybe takes nine.” But in the end, the team completed a remarkable feat. “It took everybody’s sacrifice to make that happen,” Vono said. ■
—Sonal Patel is a POWER senior associate editor.
The post Technology Triumph: Track 4A Is POWER’s Plant of the Year appeared first on POWER Magazine.